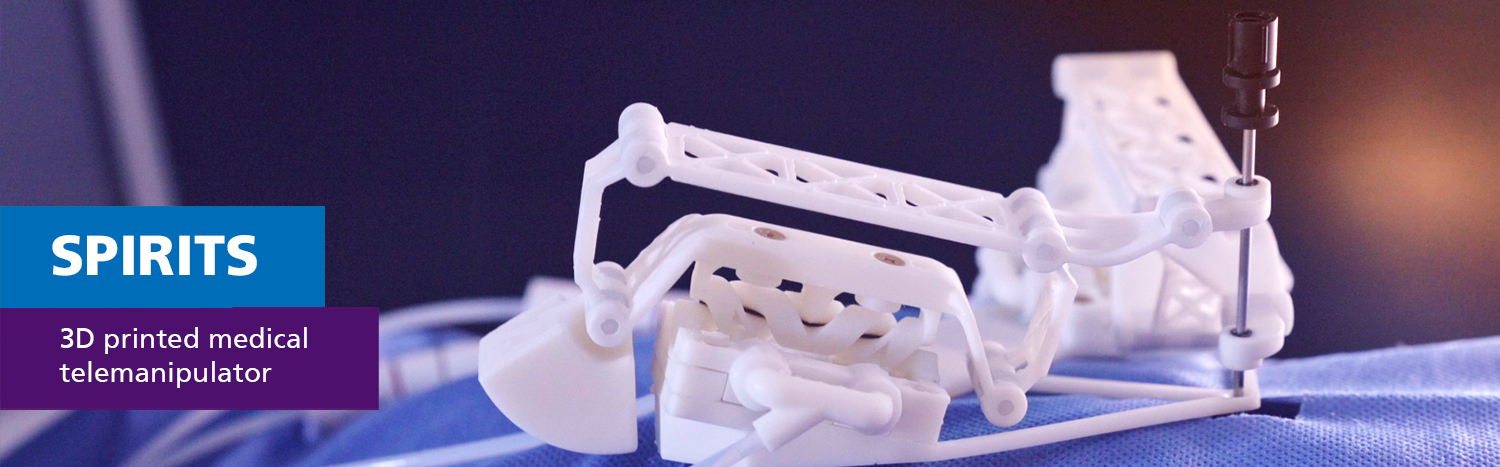
Image-guided minimally invasive surgery is at the beginning of a new era. The ever closer connection between surgical interventions and imaging techniques is creating hybrid minimally invasive techniques that promise improved interventions, reduced post-operative complications and more cost-effective healthcare.
Assistive robotic systems are already the state of the art in a number of surgical procedures. In interventional radiology, on the other hand, these systems are not yet widespread. Although a limited number of approaches exist, they lack flexibility in relation to existing imaging modalities and do not provide the necessary safety and ease of use for the physicians in the OR.
The SPIRITS project, a collaboration between the University Hospital Mannheim, ICube-INSA Strasbourg, Hochschule Furtwangen, Fachhochschule Nordwestschweiz and Ecole polytechnique fédérale de Lausanne, addresses this pressing problem.
The use of robotic systems in conjunction with various imaging techniques puts very high demands on the mechanical components: The system has to be very compact, for example to avoid collisions with a C-arm or to allow the system to be inserted into the bore of a CT or MRI scanner. Limits are also set in the selection of materials: Metallic structures would generate image artifacts, and the use of conventional electric motors in the magnetic field of an MRI is not possible.
In the SPIRITS project, almost the entire manipulator comes from a 3D printer - as a combination of rigid and flexible polymers. The project team at Fraunhofer IPA and the University Hospital Mannheim has developed a special kind of actuators for this purpose: Hydraulic actuators manufactured by polymer 3D printing and operated with water. The entire hydraulic control unit for the actuators is located in the control room. However, the manipulator, which is connected via tubes, can be located several meters away, allowing all incompatible components to be located outside of the intervention room.
The research activities in the SPIRITS project include the investigation of novel 3D printing materials with regard to their compatibility with medical imaging modalities and their suitability for medical robots and novel actuators. Within the project, a prototype with two degrees of freedom was produced using additive manufacturing. This system enables the precise positioning of a needle within the bore of a CT or MRI scanner without the attending physician having to be in the intervention room.
The SPIRITS project is supported by the INTERREG Upper Rhine programme of the European Regional Development Fund ERDF.